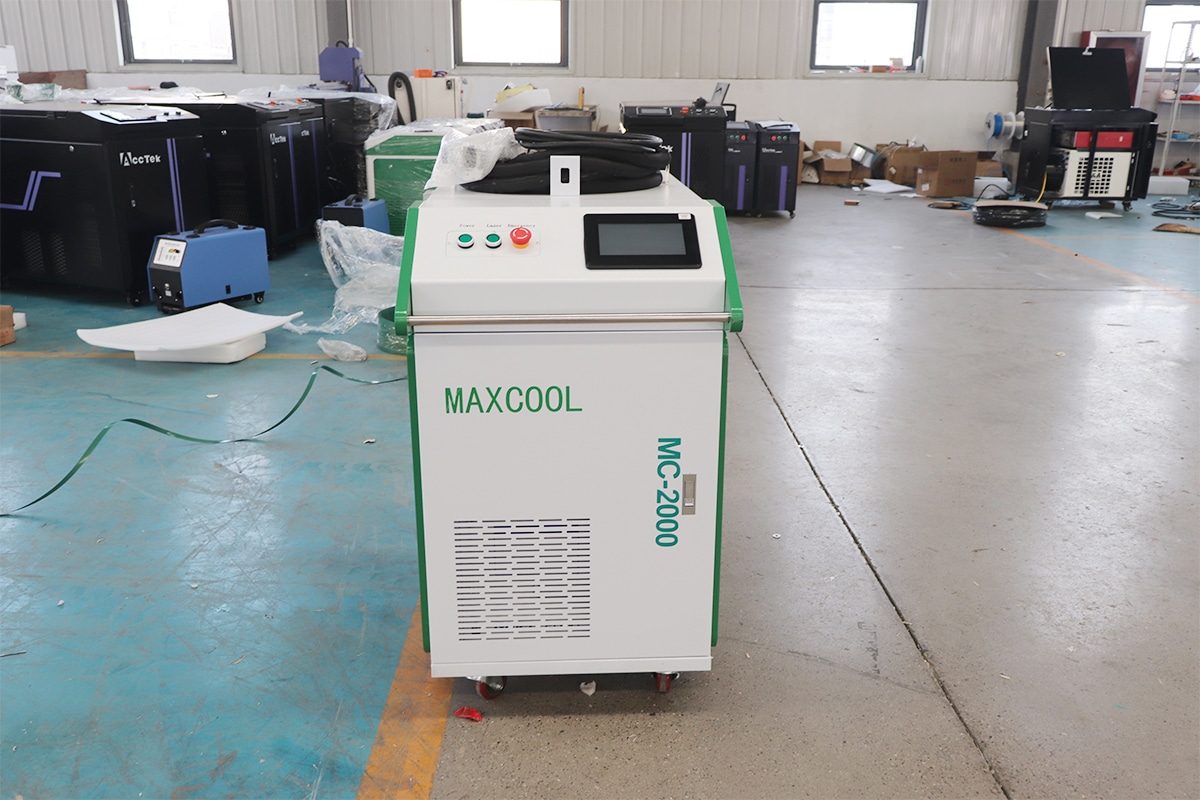
Daily Maintenance Practices
Inspecting Components: Examine the machine for visible signs of wear, damage, or contamination. Look for loose or frayed cables, cracked lenses, or damaged external parts. Ensure that all external components, such as the nozzle, protective shields, and mounts, are intact and properly secured.
Cleaning the Lens: Always power down and unplug the machine before cleaning the lens to ensure safety. Utilize a microfiber cloth and a lens-safe cleaning solution recommended by the manufacturer. Avoid abrasive materials that could scratch the surface. Do not touch the lens directly with your hands, as oils from your skin can leave residues.
Checking Power Connections: Look for frayed or damaged cables, loose plugs, or exposed wires that could pose a safety risk. Ensure all power connections are firmly plugged in and free from corrosion. Verify that the power supply is consistent and within the range specified by the manufacturer.
Weekly Maintenance Tasks
Verifying Alignment of the Laser Beam: Use a beam alignment tool or follow the machine’s alignment process as outlined in the user manual. Observe the beam path to ensure it is straight and centered. Misalignment may indicate issues with optical components or mounts. If misalignment is detected, use the machine’s adjustment mechanisms to realign the beam.
Cleaning External Surfaces: Dust, debris, and residue can accumulate on the exterior of the machine over time, potentially entering internal components and causing operational issues. Weekly cleaning of external surfaces helps maintain the machine’s integrity. Always power down the machine before cleaning to ensure safety.
Monitoring Cooling System Performance: For water-cooled systems, ensure the coolant reservoir is filled to the recommended level. Refill with the appropriate coolant if needed. Look for leaks, cracks, or blockages in the coolant lines. Tighten any loose connections. For air-cooled systems, remove and clean the filters to ensure proper airflow. Replace filters if they show signs of wear or damage.
Checking the Air Filtration System: Check for signs of clogging or saturation in the air filters. Remove and clean reusable filters according to the manufacturer’s guidelines. Replace disposable filters when they are full or damaged. Ensure that the airflow is unobstructed and that the filtration system is effectively capturing debris and fumes.
Monthly and Periodic Maintenance
Deep Cleaning the Optical Components: Utilize optical-grade cleaning solutions, lint-free wipes, and blower brushes to safely clean lenses and mirrors without causing scratches or damage. Check for cracks, chips, or other damage to the optical components. Replace any compromised parts immediately. After cleaning, verify the alignment of the optical system to ensure accurate laser delivery.
Lubricating Moving Parts: Moving parts such as mounts, hinges, and adjustable mechanisms are subject to wear and tear due to frequent use. Refer to the machine’s user manual to identify which parts need lubrication. Use manufacturer-recommended lubricants to avoid compatibility issues or damage. Apply a small amount of lubricant to the moving parts and wipe away excess to prevent dirt accumulation.
Calibrating the Machine: Refer to the user manual or calibration software for detailed instructions on how to perform the process. Utilize any included calibration targets or tools to measure the accuracy of the laser’s output. Test the machine on sample surfaces to verify the beam’s precision and cleaning effectiveness.
Inspecting and Updating Software: Visit the manufacturer’s website or contact Maxcool CNC to check for software updates or patches. Before updating, back up the current machine settings and configurations to avoid data loss. Follow the manufacturer’s instructions to safely download and install software updates. Run the machine to ensure it operates correctly with the updated software.
Maintaining laser cleaning machines is essential for ensuring their optimal performance, longevity, and safety. Regular maintenance practices, such as daily inspections, cleaning lenses, checking power connections, and running diagnostics, help prevent minor issues from escalating into costly repairs. Weekly tasks, including verifying beam alignment, cleaning external surfaces, and monitoring cooling and filtration systems, keep the machine running efficiently and reduce downtime. Monthly and periodic maintenance involves deep cleaning optical components, lubricating moving parts, calibrating the machine, and updating software to maintain precision and reliability. By integrating these maintenance practices into a routine, users can maximize the performance, efficiency, and lifespan of their laser cleaning machines, safeguarding their investment and ensuring superior cleaning results.